
Imagine this: you’ve invested countless hours into creating an exceptional board game. The gameplay is engaging, the artwork is captivating, and you’re eager to share it with the world. However, one final challenge stands in your way: mass production.
Don’t worry, we’re here to guide you through this exciting journey, ensuring you come out on top with your game on store shelves and in the hands of enthusiastic players. In this guide, we’ll shed light on the entire process, providing actionable advice and insights on how to mass produce board game pieces that lead to success.
Key Takeaways
- Understanding the mass production process for board games.
- Cost breakdown and budgeting tips.
- Step-by-step guide to mass-producing your board game pieces.
- Real-life success stories and best practices.
Contents
Current Trends in the Production of Board Games

In the constantly evolving world of board games, efficiency is crucial. Manufacturers continually seek methods to produce large quantities of game components at a cost-effective rate. It’s about finding the perfect balance between quality and affordability.
Mass production offers several benefits, such as lower costs per unit, consistent quality, and quick fulfillment of large orders. However, it also presents challenges, including significant initial investments and managing extensive inventories. Learning how to mass produce and sell the best board games effectively is crucial for success in this competitive industry.
Consider the story of Bear Mountain Camping Adventure. They navigated these challenges by partnering with experienced manufacturers and utilizing crowdfunding to reduce initial costs. Their success highlights the importance of strategic planning and expert collaboration. By working closely with seasoned professionals and leveraging platforms like Kickstarter, they minimized financial risks and maximized their reach to potential backers, showcasing the power of community support in bringing a board game to life.
How Do You Manufacture a Board Game?
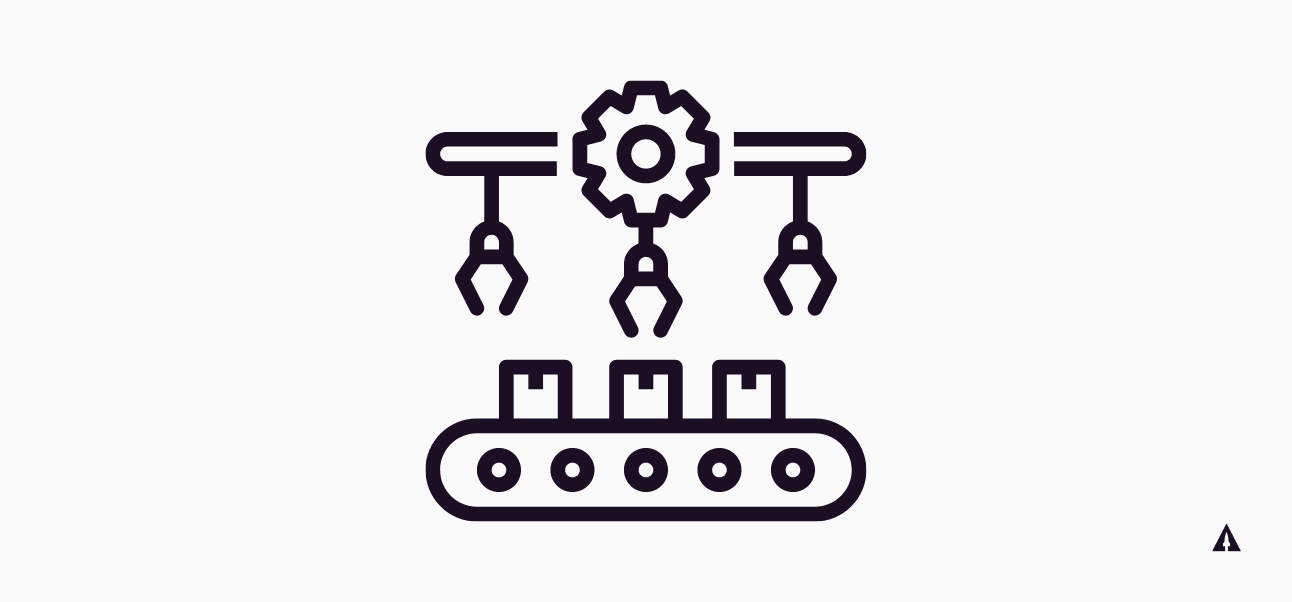
Manufacturing a board game is like embarking on a well-planned adventure. Each stage is essential to your ultimate success, and understanding the intricacies of board game manufacturing is key to ensuring a smooth process from start to finish. When you’re looking into how to mass produce board game pieces, consider the following stages:
- Design and Prototyping: Start by finalizing your game design and creating prototypes to test gameplay and materials. This phase involves multiple iterations of game mechanics and aesthetics to ensure everything works seamlessly together. Use playtesting sessions to gather feedback and make necessary adjustments to improve the overall experience.
- Sourcing Materials: Select the best materials for durability and aesthetic appeal. Quality components, such as sturdy cards, vibrant prints, and durable tokens, enhance the player’s experience and longevity of the game. Building relationships with reliable suppliers can help secure high-quality materials at competitive prices.
- Production: Proceed with mass-producing game pieces using methods like injection molding, printing, and cutting. Each method has its own set of considerations. Injection molding, for example, is ideal for plastic components but requires significant upfront investment in molds. Printing techniques for cards and boards should focus on color accuracy and finish.
- Quality Control: Ensure each piece meets quality standards. Establish rigorous quality control procedures to catch defects early. This might include visual inspections, functionality tests, and stress tests for durability. Consistent quality ensures that every game delivered to customers meets their expectations.
- Packaging and Distribution: Finish by preparing your game for shipment and distribution, ensuring it reaches customers in perfect condition. Design packaging that protects components during transit and appeals to consumers on the shelves. Efficient logistics planning can streamline distribution and reduce costs.
Alpha Clash, another successful board game, raised over $481,000 on Kickstarter. Their commitment to detailed design and rigorous quality control helped them surpass their fundraising goals, demonstrating the importance of meticulously following these steps. Their thorough approach to each stage, from initial design to final distribution, serves as a valuable blueprint for aspiring game creators.
How Much Does It Cost to Mass Produce Board Game Pieces?

The cost to mass-produce board game pieces varies significantly, depending on several factors:
- Design and Prototyping: Expenses involved in designing and testing your game. These costs can include graphic design, artist fees, and playtesting materials. Investing in high-quality design can make a significant difference in the game’s appeal and marketability.
- Tooling and Setup: Initial costs for setting up production machinery. This includes creating molds for plastic pieces, printing plates for cards, and cutting dies for board components. These are often one-time costs but vary depending on the complexity of your game.
- Production Costs: Variable costs per unit, which typically decrease as volume increases. Bulk ordering materials and negotiating long-term contracts with manufacturers can help reduce these expenses. Production costs also encompass labor, energy consumption, and waste management.
- Packaging: Expenses related to designing and producing game boxes and inserts. Packaging not only protects the game but also serves as a marketing tool. Investing in visually appealing and sturdy packaging can enhance the unboxing experience and boost sales.
- Shipping and Logistics: Costs associated with distributing the finished products to customers. This includes warehousing, handling, and transportation fees. Partnering with reliable logistics providers and optimizing shipment sizes can reduce these costs.
Biome invested in quality materials and production processes, enhancing player satisfaction and encouraging repeat purchases. Their focus on durability and aesthetic appeal helped build a loyal customer base, proving that investing in quality pays off in the long run.
Steps to Mass Produce Your Board Game Pieces

Detail Your Costs and Numbers
Begin by calculating all production costs, including design, materials, manufacturing, and logistics. Use detailed spreadsheets to track these expenses and forecast profits. This financial planning is crucial for securing funding and managing budgets effectively. Consider potential cost fluctuations and include contingency funds to cover unexpected expenses.
Check and Finalize the Design
Before ramping up production, finalize your game design to avoid costly changes later on. Thoroughly test prototypes and gather feedback for necessary adjustments. This phase should also include thorough rulebook editing and ensuring all components align with the final design vision. Clear, comprehensive rules enhance the player experience and reduce customer service inquiries post-launch.
Botany benefited from ensuring their designs were finalized before production, saving time and resources. Their meticulous approach to design iteration and user feedback collection helped streamline the production process and minimize last-minute changes.
Make Your Prototype
Develop a prototype to assess the game mechanics, material quality, and overall design. This prototype can also help attract backers or investors. High-fidelity prototypes that closely resemble the final product provide a tangible preview to potential supporters and can be used in marketing campaigns and trade shows.
Philharmonix demonstrated the critical role of this step by refining their design and securing funding through Kickstarter. Their polished prototypes showcased the game’s potential, generating excitement and trust among backers.
Prepare for Mass Production
Collaborate with manufacturers to set up your production processes. Ensure they understand your quality standards and timelines. Detailed production schedules and clear communication channels are essential. Regular updates and visits to the manufacturing site can help monitor progress and address any issues promptly.
Alpha Clash effectively selected manufacturing partners who could meet their high standards and tight schedules. Their proactive approach to partnership and quality assurance ensured that the final products met their expectations and delighted customers.
Start to Sale
After production, focus on marketing and sales strategies. Utilize platforms like Kickstarter to broaden your audience and secure pre-orders. Effective pre-launch marketing, including social media campaigns, email newsletters, and influencer partnerships, can build momentum and ensure a successful launch. Check out our detailed guide on how to kickstart a board game for effective strategies.
Surviving Strangehollow showcased the effectiveness of a robust pre-launch strategy and engaging marketing efforts by funding his campaign goal on the first day of this campaign. Their well-planned marketing blitz created a sense of urgency and excitement, driving early support and word-of-mouth promotion.
Final Thoughts
Mass-producing board game pieces is a significant undertaking that requires detailed planning, budgeting, and execution. But don’t be intimidated, dedicated creator! By following this guide on how to mass produce board game pieces and learning from the experiences of successful creators, you can navigate this process and bring your game to eager players.
Ready to start your board game production journey? Book a call with a LaunchBoom expert today for personalized guidance and support. Together, we’ll help turn your board game vision into a reality!
Mass Producing Board Game Pieces: Frequently Asked Questions
How Are Board Games Produced?
Board games are produced through a series of steps, including design, prototyping, sourcing materials, manufacturing, quality control, packaging, and distribution. Each stage brings you closer to your ultimate goal.
Can You Make a Lot of Money Creating a Board Game?
Yes, successful board games can be highly profitable. Examples like Botany and Alpha Clash demonstrate that with effective marketing and quality production, creators can achieve significant earnings.
How Long Does It Take to Manufacture a Board Game?
The timeline for manufacturing a board game can vary, but it typically takes several months from design to final production. Factors include the complexity of the game, production volume, and the efficiency of your manufacturing partners.